건설용 강재개발 및 용접기술동향
Development of Structural Steel and Trend of Welding Technology
Article information
Trans Abstract
A brief overview is given of the development of various structural steels and their welding application technology. Firstly, the general characteristics and welding performance of structural steels used in architecture and bridge are introduced. For safety against earthquakes or strong wind, and for highly efficient welding in high-rise building constructions, ultra high strength steel with tensile strength over 800 MPa or high HAZ toughness steel plates under high heat input welding have been developed. In particular, efficient welding technology ensuring high resistance to cold and hot cracking of ultra high strength steel is reviewed in the present paper. Secondly, various coated steels used mainly for outer part in construction are briefly discussed. Moreover, a major drawback of coated steel during welding operation, and several solutions to overcome such technical problem are proposed. It is hoped that this review paper can lead to significant academic contributions and provide readers interested in the structural steels with useful welding technology.
1. 서 론
현대의 초고층, 초대형 빌딩 및 장대교량과 같은 철골조 건축구조물을 건설하고 유지하기 위해서는 우수한 기계적 물성의 건축구조용 강재개발과 함께 철강 건축 부재의 제작효율 향상을 위한 효과적인 용접이용 기술의 확보가 필수적으로 요구된다.
우선, 초고층 빌딩 건설이 증가하면서, 극후물 강재의 수요가 증가하고 있다. 즉 건축구조물이 대형화되면서 사용되는 구조부재의 단면이 증가하여, 80mm 혹은 100mm 두께의 후물 강재가 요구되며, 이에 따라 판 두께 방향에 대한 물성보증 및 높은 저온균열 저항성이 확보되어야 한다. 강재의 극후물화는 곧 부재 제작의 효율성 향상이라는 측면에서 대입열 용접용 강재 및 용접이용 기술이 개발되어야 할 것이다. 일본의 경우, 1970년도부터 대입열용 강재개발을 주도하여, 현재는 후물 구조용 강재의 경우에도 SAW (Submerged Arc Welding)기준으로 600 kJ/cm, ESW (Electro-Slag Welding) 기준으로 1000 kJ/cm의 대입열 용접이 범용적으로 적용되어 주로 1 Pass로 용접을 마무리하고 있다. 반면, 국내의 경우, POSCO社에서 SAW 200 kJ/cm을 목표로 대입열용 강재를 개발하였지만, 국내 건축분야에 적용된 사례는 전무한 실정이다.
구조물에 강재를 적용하는 측면에서는 보다 고강도급의 강재를 적용하여 전체 소요물량의 저감을 통한 경제성을 확보가 필요하다. 이에 따라 국내의 경우, 800 MPa급의 초고강도 강재를 개발하여 최근, 롯데월드타워, 인천공항 제2여객터미널 등에 적용하여 기존 570 MPa급 강재에 비해 대략 30%의 물량저감 효과를 가져온 바 있다. 일본의 경우, 최근 1000 MPa급 초고강도 강재를 최초로 개발하여 Obayashi 기술연구소 건물의 Box Column 부분에 적용한 바 있다1). 구조물의 안전성 측면에서는 내진설계 시 소성변형을 허용하는 SN 강재를 비롯하여 저 항복비 (YR: Yield Ratio)를 만족하는 강재의 개발 및 적용이 이루어지고 있으며, 화재와 같은 고온에서도 일정시간 이상 고온강도를 유지하여 내화피복의 사용을 생략할 수 있는 내화강이 개발되었다. 하지만 국내의 경우, 개발된 내화강재에 적용할 수 있는 국산 용접재료가 전무하여, 용접부 성능평가를 위해 외산 용접재료를 수입하고 있는 실정이다. 강구조물의 장수명화 측면에서는 고내식 교량용 내후성강 및 건축외장용 도금강판의 개발 및 적용이 이루어지고 있다. 즉, 염화이온이 존재하는 대기 환경 하에서 강재 표면에 치밀한 부식생성물을 형성시켜 부식의 진행을 억제시키는 내후성강과2), 철보다 전위가 낮아 활성금속으로 알려져 있는 아연 혹은 아연, 알루미늄, 마그네슘 등의 합금을 도금하여 희생양극 효과로, 소지 철의 적청발생시간을 지연시키는 고내식 도금강판 등3,4)을 지속적으로 개발하고 적용하려는 시도가 이루어지고 있다.
앞서 언급한 건축구조용 강재는 일반적으로 노멀라이징 (Normalizing), 퀜칭/템퍼링 (Quenching/Tempering), TMCP (Thermo-Mechanical Controlled Process) 등으로 제조되고 있고, 현재 TMCP 제조기술이 가장 보편적으로 활용되고 있다. 따라서 본 기고에서는 현재 고성능 강재 제조공정에 활용되고 있는 TMCP 제조기술, 건설 및 교량용 강재, 용접이용 기술 등을 중심으로 국내와 일본을 비교하여 논의를 진행하고자 한다.
2. 건설용 강재 제조공정
본 절에서는 건설용 강재의 대표적인 제조공정인 TMCP에 대해 간략히 소개하고자 한다. TMCP는 결정립 미세화와 미세조직 제어를 위해 제어압연과 가속냉각을 적용한 공정으로, 재결정영역에서 압연하는 종래의 후판강 압연공정과 달리, 미재결정영역에서 압연함으로써 오스테나이트 결정립 내부에 변형띠를 생성시켜 추가적인 핵생성 자리를 형성시켜 미세조직 및 물성을 제어하는 것이 특징이다5). Fig. 1에서 As-rolled, Normalized 및 TMCP를 통해 형성된 각 미세조직을 비교하여 나타내었다. As-rolled와 Normalized 된 경우, 강재의 강도증가를 위해서는 탄소, 망간 등의 합금성분을 증가시키는 것이 필요하지만, TMCP 공정의 경우, 추가적인 합금 첨가나 후열처리 없이 미세조직 제어를 통해 고강도 및 고인성의 물성을 확보할 수 있다. 따라서, 저합금계 성분에 따른 저 탄소당량 임에도 불구하고, 고강도 강 제조가 가능하며, 우수한 용접성을 바탕으로 활용도가 높은 것으로 평가 받고 있다5).
해외의 경우, 특히 JFE社 공정설비의 경우, 국내의 TMCP 공정과 유사하되, 인장강도 690 MPa급 이상의 고강도 강재제조 시 Heat treatment Online Process (HOP)를 위한 별도의 설비를 갖추고 있다6). 유도가열을 통해 A1 온도 이하에서 20 °C/s의 급속 승온 및 냉각을 통해 조직 내, 특히 입계에 석출되는 Fe3C의 응집을 막고, 미세한 형태로 분산시킴으로써 물성향상에 기여할 수 있다. Fig. 2는 일반적인 Tempering을 통해 형성된 응집된 Fe3C 형태와 On-Line Accelerated Cooling (OLAC) 및 HOP를 통해 미세분산된 Fe3C 형태를 비교하여 나타내었다7). 특히 상온에서 저 탄소의 템퍼드 베이나이트와 미세 분산된 M/A 생성물 (Martensite/Austenitie constituent)을 복합적으로 형성시킴으로써 690 MPa급 이상의 고강도 강재를 개발한 바 있다6,7). 일반적으로 미세조직 내 M/A 생성물의 형성은 충격인성 등의 특성에 악영향을 끼치는 것으로 알려져 있지만, M/A 생성물이 미세한 크기로 분산될 경우, 충격인성 저하에 큰 역할을 하지 않으면서 강도향상에 효과적으로 기여할 수 있는 것이다. 이와 같은 고강도 강재개발의 기본 개념은 다음과 같다. 우선, 가속냉각 후 베이나이트 시작 및 종료 온도 사이에서 유지시켜, 미세조직을 베이나이트와 잔류 오스테나이트 (RA) 복합조직을 형성시킨 후, HOP을 통해 A1 온도 이하에서 템퍼링하여 냉각시키면, 베이나이트 내에 과포화 되어있던 탄소가 확산하여 배출되고, 탄소가 유입된 잔류 오스테나이트 의 경우 경화능이 높아져 상온으로 냉각시, M/A 생성물로 변태된다. 결국, 템퍼드 베이나이트와 대략 13% 정도의 미세분산 된 M/A 생성물의 복합조직이 형성되는 것이다. Fig. 3와 4는 각각 HOP 적용을 통한 고강도급 강재의 미세조직 형성과정과 강재의 CO2 용접부 성능 등을 보여준다.
3. 건축구조용 강재 / 용접기술
Table 1은 국가별 건축용 강재개발 현황을 각 규격과 함께 보여준다. 우선, 일본 JIS (Japanese Industrial Standard) 규격 강재의 경우, 지진에 취약한 일본의 특성상, 내진설계 된, 즉 저 항복비 개념으로 개발된 강재가 많다. 한국 KS (Korean Industrial Standard) 규격의 경우, 과거 JIS 규격에 등재된 강재의 대부분을 KS 규격으로 옮겨서 등재시켰기 때문에, JIS 규격과 큰 차이는 없지만, PILAC BT (POSCO InLine Accelerated Controlled-Building high Tensile) Series 및 HSA (High strength rolled Steel for Architecture) 800 강재 등으로 POSCO社 내에서 독자적으로 개발한 강재가 최근 KS 규격으로 새로이 등재되어 적용되고 있다. 반면, 미국 ASTM (American Society for Testing Materials)이나 유럽 EN (European Standards) 규격의 강재를 살펴보면, 탄소당량에 대한 규제가 거의 없거나 그 상한치가 국내 또는 일본에 비해 높은 수준이며, 항복비에 대한 규제도 사실상 없고, 일부 규격 (ASTM A992)의 경우 항복비 < 85%로 규정되어 있을 뿐이다 (Table 내 붉은색 표시: 항복비가 규정된 강재). 즉, 용접성 및 내진성능에 대한 고려가 일본 및 국내의 경우에 비해 엄격하지 않은 수준이다. 특히, 일본의 경우 현재 1000 MPa급의 초고강도 강재를 개발하여 ’13년도에 Obayashi 기술연구소 건물의 Box Column 부재로 적용한 바 있다1). 강재개발과 적용 용접법 등은 다음 절에서 소개하고자 한다.
3.1 SM 강재
과거, 국내 개발된 SM490급 강재의 경우, 구속응력이 높은 구조물의 경우 용접열영향부 (HAZ)에서 층상 형태의 라멜라테어가 빈번히 발생하기도 하였고, 이를 극복하기 위한 방안으로 강재의 청정도 관리 (Ca/S 비율)와 함께 구속응력의 분산을 목적으로, 1회 용착량 제한, Balanced 용접시공, 판 두께방향으로 향하는 응력의 분산법 등 효과적인 용접시공 기술 또한 개발되어 왔다. 특히, POSCO社 개발강종인 PILAC-BT 33, 36, 45의 경우, SN490C 강재와 같이, 판 두께방향 인장실험 단면수축률 (%)의 하한치를 규정하여 라멜라테어 저항성 보증을 원칙으로 하고 있다. 최근 개발되는 SM490 강재는 기본적으로 용접성을 고려하여 탄소, 인, 황의 상한치를 규정하고 있고, B, C 등급 (SM490 강재의 경우, A, B, C 등급으로 구분되며 각 등급마다의 요구 물성치가 상이함)에 한정하여 충격인성 하한치를 명시하고 있으며, 라멜라테어 저항성 평가에 널리 활용되었던 Cranfield 용접균열 평가와 Window Type 용접균열 평가 결과, 균열이 용이하게 발생하지 않게끔 강재의 청정도 관리수준이 향상된 것으로 평가되고 있다.
국내의 경우, Built-Up H 부재 제작의 90% 이상을 SM490A 급 강재를 적용하여 범용적으로 사용하고 있는데 반해, 지진 발생이 많은 일본의 경우, 저 항복비 개념으로, 소성변형을 허용하는 내진설계 하에서 개발된 SN490C급 강재가 주로 적용되고 있다. 내진강재로 알려져 있는 SN 강재는 다음 절에서 구체적으로 설명하고자 한다.
3.2 SN 강재
내진성능 향상을 위해 저 항복비 (80% 이하)로 설계된 강재로서 주로 일본 건축공사에 적용 빈도가 높으며, 용접성을 고려하여 탄소, 인, 황의 성분 상한치와 함께, 탄소당량과 용접균열지수 (Pcm)의 상한치도 함께 규정되어 있다. 또한 C 등급재의 경우, 판 두께 방향 인장실험 단면수축율을 25% 이상을 요구하고 있다. 강재의 인장강도 대비 항복강도의 비율, 즉 항복비 값을 80% 이하로 설계한 것은, 지진과 같은 외력 발생시 강재의 소성변형이 시작되는 시점부터 최종 파단에 이르기까지의 시간적 여유를 확보하여 인명피해를 최소화시키고자 함에 있다. 항복비 값을 낮추기 위한 야금학적인 방법으로는 우선 다상 조직의 확보를 생각해 볼 수 있다. 경한 단상조직에 비해 연한 조직과 경한 조직이 공존할 때 항복비 저감 효과가 큰 것으로 알려져 있고, 미세조직 내 M/A의 미세분산 또한 항복비 저감에 효과적인 것으로 보고되고 있다7,8). 일본 JFE에서 생산된 HBL385급 강재의 경우, GMAW (Gas Metal Arc Welding), FCAW (Flux Cored Arc Welding), SAW 등의 용접 프로세스 적용을 통한 물성보증 측면에서 층간온도와 입열량 상한치를 각각 250~300 °C, 30~40 kJ/cm로 소개하고 있다. 입열량과 층간온도가 높아지면 용접금속 및 조대결정립 열영향부 (CGHAZ)의 충격인성이 저하되는 것이 일반적이나, HBL385급 강재에 각 용접 프로세스에 적절한 용접재료를 적용하였을 때, 30~40 kJ/cm 수준의 입열과 250~300 °C의 층간온도까지 물성보증이 가능하게끔 강재 및 용접재료를 개발하였다. 최근 POSCO社에서 자체 개발한 PILACSN385급 강재의 경우에도 HBL385급 강재와 유사한 수준으로 개발하여 일본 국토교통성 대신 인증서를 획득하여 일본 수출을 위한 교두보를 마련한 바 있다.
3.3 초고강도 강재 (TS: 800 MPa급 이상)
초고강도급 강재의 용접부 성능에 있어 가장 중요한 문제는 용접부에서 발생하는 저온균열이다. 용접 시 대기 중, 혹은 용접 플럭스 내 존재하는 수분이 용접열에 의해 열분해되어 용접부 내로 유입되는 확산성수소와, 용접 후 필연적으로 발생하는 응고수축에 따른 구속력, 그리고 경화조직에 의해 발생하는 저온균열은 강재의 강도에 따라 그 민감도가 증가하는 것으로 알려져 있다9). Fig. 5 (a)는 일반적인 용접부 저온균열의 발생양상과 (b) 실제 HSA800 강재 용접부에서 발생한 횡균열을 보여준다. 물론, 용접재료 내, 인, 황, 보론 등의 성분이 높거나, 개선각이 좁은 경우, 주로 초층용접 시 Form factor (Form factor (%) = Width/depth × 100)가 낮아 고온균열이 발생 (Fig. 6) 할 수 있지만, 이 경우, 용접재료 내 적절한 합금설계와 함께 초층용접 시, 상대적으로 저 강도, 고 인성의 용접재료를 적용하되, 입열을 낮추어 용착량을 줄이거나 개선각을 증가시키는 방식으로 극복 가능하다.
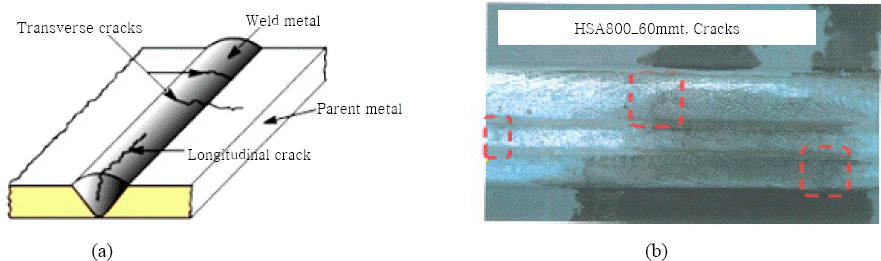
(a) General behavior of cold cracking and (b) Transverse cracks in weld metal of HSA800 with 60mm thickness
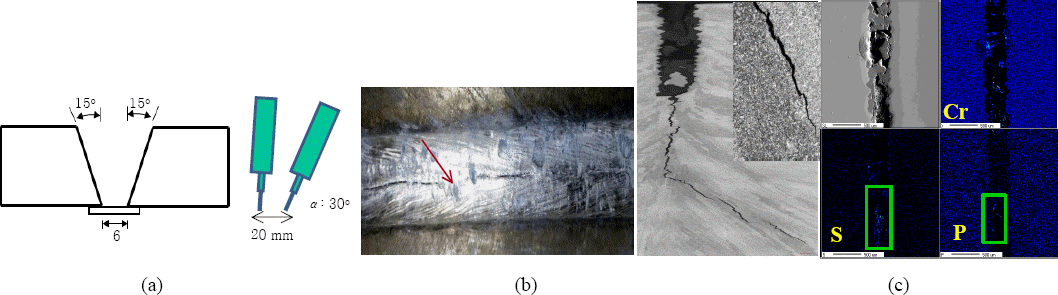
(a) Welding conditions and (b) Observation of hot cracking right after the root pass in SAW, and (c) Elemental data analyzed by EPMA
TS 800 MPa 이상의 초고강도 강재의 특성상 용접부 Overmatching을 위한 용접재료 설계 시, 필연적으로 고합금계 성분으로 재료를 설계한다. 이 경우, 마르텐사이트 변태시작온도 (MS 온도)가 낮아져, 용접 후 냉각 시 상대적으로 오스테나이트 조직으로 머무는 영역이 커지는 효과를 가져온다9). 즉, 용접 시 용접금속으로 유입된 수소원자는 FCC 구조 내에서 그 용해도가 BCC 구조에 비해 훨씬 높으며, 반대로 확산계수는 BCC 구조에 비해 극히 낮다10). 따라서, 고합금계 용접금속 내에서 수소원자는 안정적으로 머물 수 있고, 상온으로 최종 응고 시, 결국 BCC 구조로 변태된 용접금속 내에 수소원자가 다량으로 존재하여 조직의 취화 및 균열을 발생시킨다. 즉, 저강도급 강재의 경우, 저온균열이 빈번히 관찰되는 영역이 HAZ인데 반해, 고강도급 강재일수록 용접금속 내에서 저온균열이 더욱 빈번히 발생하는 것이다. 따라서 TS 800 MPa 이상의 초고강도 강재를 건축구조물에 효과적으로 적용시키기 위해서는 확산성수소량이 극히 낮은 저수소계 (통상 4 ml/100g 이하) 용접재료로 설계해야 하며, 복합와이어의 경우 내부 흡습이 되지 않도록 Seamless로 개발할 필요가 있다. Fig. 7은 국내 Poswelding社에서 개발한 SAW용 Seamless 복합와이어의 단면 형상을 보여주며, 가스 크로마토그라피 (Gas chromatography) 방식을 통해 측정한 확산성수소량을 나타내었다.
국내 POSCO社에서 개발한 HSA800 강재의 경우 TMCP로 제조하였으며 미세조직은 베이나이트로 구성되어 비커스 경도값이 대략 260~290 hv 정도이며, 탄소당량과 용접균열지수가 각각 0.5와 0.198 정도의 수준으로 KS D 5994 규격의 상한치를 만족한다. 최근 동대구역사, 서울대 관장도서관, 제2롯데월드타워 등의 건설에 HSA800 강재가 적용되어 용접 시공되었고, 주로 FCAW 및 SAW가 적용되었다. 특히 SAW의 경우, 1 Pole 용접으로 입열량을 35 kJ/cm 이하로 제한하였으며, 예열의 경우, 균일하게 예열되는 효과를 위해 예열패드를 부착하여 60mm 판재 기준으로 150 °C의 온도로 예열관리를 함으로써 저온균열의 발생을 방지하고자 하였다. 입열량을 50 kJ 이상으로 높여 적용하게 되면, 고강도 TMCP 강재의 특성상 HAZ 연화현상으로 인해 강재의 최소요구강도인 800 MPa을 확보하기 힘들다. 최근에는 Tandem SAW를 위한 용접재료 및 용접조건을 최적화하여 생산성을 향상시키고자 하는 노력이 지속적으로 이루어지고 있다. Fig. 8는 Tandem SAW를 위한 용접조건 및 충격인성 평가 결과를 보여준다.

(a) Welding conditions for high speed tandem SAW and (b) Its impact toughness values evaluated at 0 °C
한편 일본의 경우, 초고강도급 강재 (1000 MPa)를 Box Column 등에 적용하되, 고 YR로 설계하여 지진과 같은 외력 발생 시, 압축응력만이 부가되며, 횡력에너지 흡수를 위해, 대부분 저강도, 고연성의 저항복점 강재 (LY100, LY225)를 내진 Damper로 적용하고 있다1). Fig. 9는 최근 NSSMC의 건설용 강재 적용현황을 보여준다. 즉, 일본 내 크고 작은 지진을 겪으면서, 지진 후 소성변형 된 건축물의 재건과 관련한 어려움으로 인해 부재 설계 방식이 변경된 것이다. ’13년경 일본 Obayashi社 기술연구소 건물 건설에 Box Column 부재로 NSSMC에서 개발한 인장강도 1000 MPa급인 HT880 강재가 최초로 적용되었다. 기존 490급 강재대비 항복강도가 2.7배 정도 높은 수준이고, 고 항복비로 설계한 강재로, 미세 템퍼드 마르텐사이트의 미세조직을 형성하고 있다. Fig. 10에서 알 수 있듯이, Box column 제작을 위한 용접 시, 부분용입하여 시공을 간소화하되, 초층은 상대적으로 저강도급 재료 (YGW 11, JIS Z 3312)를 적용하고, 후층부터는 1000 MPa급 재료를 적용하였다11). 일반적으로는 완전용입을 적용하여야 하나, 부분용입이 가능하려면 설계 시 지진이 발생한 경우에 각 용접부에 요구되는 전단내력의 크기를 모사하고, 부분용입 적용 시 필요 목 두께 등을 결정하여야 한다. Table 2 (a)는 용접 시 적용한 용접재료 및 조건을, 그리고 (b)에서 용접부 및 HAZ 충격인성 값을 나타내었다. 한편, 일본 Tomoya를 비롯한 연구자들은 1000 MPa급 강재의 건축분야 적용 가능성을 GMAW 및 SAW 프로세스로 평가하여 학계에 보고한 바 있다12). 본 연구에 따르면, 용접 시 보호가스 내 CO2 함량이 증가하면 아크 내에서 해리되는 산소량이 증가하고, 망간, 실리콘 등의 성분과 산소가 반응하여 산화물을 형성하는 방식으로 강 내 망간, 실리콘 등의 성분 수율 및 경화능이 감소하여, 결과적으로 강도저하와 산화성 개재물 증가로 충격치가 감소할 수 있다. Table 3은 본 연구에서 제안한 GMAW 및 SAW의 용접조건을 나타내었다
3.4 대입열용 강재
현대 건축구조물의 설계 방향이 초고층화 됨에 따라 적용 강재 또한 점차 후육화되고 시공생산성 측면에서 대입열 용접에 대한 수요가 증가하고 있다. 실제로 1970년대부터 일본을 중심으로, 대입열용 강재 개발이 지속적으로 이루어졌고, 현재까지 지속되고 있다. Fig. 11은 대입열용 강재 개발의 시대별 추이를 보여준다13). 일반적으로 대입열 용접이 적용될 경우, HAZ의 결정립이 성장하고, 입계에서는 주로 입계 페라이트 및 페라이트 사이드 플레이트가 형성되고, 입내에서는 상부 베이나이트 등이 형성되어 충격인성 등의 기계적 물성을 저하시키는 것으로 알려져 있다. 따라서, 1970년부터 TiN 석출물의 입계 Pinning 효과로 결정립을 미세화 시키고자 하는 노력이 이루어졌고, 1990년대 들어서, TiO를 적용하여 입내에 페라이트의 핵생성을 촉진하여 Intergranular 페라이트를 형성시키고자 하였으며, 2000년도에는 칼슘, 마그네슘을 포함하는 Oxide/Sulfide를 활용하여 결정립 미세화 효과를 극대화시키고자 하였다. 용접 시 Fusion line 영역은 1400 °C로 온도가 상승하여 TiN의 석출물의 경우 쉽게 용해되어 Free N이 형성됨에 따라 결정립 미세화 효과가 충분하지 못하다는 문제점이 지적되어, 일본에서는 보다 열적으로 안정한 미세 Oxide/Sulfide를 활용하기 시작하였다14). Fig. 12는 TiN 석출물과 Oxide/Sulfide의 각 형태와 γ-결정립의 성장 정도를 비교하여 나타내었다. 일반적으로 Pinning 효과에 따른 결정립 성장은 다음과 같이 설명될 수 있다15).
R: 결정립 반지름, r: 2차상 입자의 반지름, f: 2차상의 부피율
즉, 미세한 2차상 입자의 분율이 높을수록 입계 Pinning 효과가 증가하여 결정립 미세화 효과가 커지는 것이다. 즉, 1400 °C의 고온에서 상당량의 TiN 입자가 용해되어 결정립 Pinning 효율이 감소되는 것이다.
한편, Yamamoto, Takamura 등의 연구자는 TiO가 본질적으로 Cation vacancy를 내포하며, 망간이 Vacancy 내로 흡수되어 주변영역에 결핍 영역을 형성한다고 보고한 바 있다16). 즉, γ상의 안정화원소인 망간의 결핍은 페라이트 변태를 촉진하여 IGF의 분율을 증가시켜 인성 향상에 기여하는 것이다. 강 내 망간의 함량이 1% 감소하면 γ → α로의 변태온도가 대략 50K 정도 상승하는 것으로 보고되어 있다. 또한 일반적으로 HAZ 인성향상을 위해 첨가하는 니켈에 비해 망간의 경우, 구 γ 입계에 편석되는 정도가 보다 높아, 입계 페라이트의 형성을 억제하는 효과가 제안되기도 하였다. Fig. 13 (a)는 (Ti,Mn)-Oxide 계면 망간 결핍영역과 (b) 입계에 망간의 편석되는 정도와 미세조직을 니켈의 그것과 비교하여 나타내었다.
뿐만 아니라 일본 JFE에서는 용접재료 내 B을 소량 첨가하여, 대입열 용접 시 용접금속에서 조대결정립 열영향부로 확산하여 BN를 형성할 수 있음을 보고하였다17). 용접금속으로부터 조대결정립 열영향부로 확산된 보론이 정확히 BN의 형태로 존재하는 지와, 결정립 미세화의 효과에 대해서는 명확히 검증되지 않은 것으로, 본 기고에서는 구체적인 언급을 제외하고자 한다.
국내의 경우, 최근 POSCO社에서는 중질소와 저 실리콘 설계에 기반한 대입열용 HSA500 강재를 개발한 바 있다. 입내 미세 TiN을 분산시켜 HAZ 결정립 성장을 억제하고, Si을 저감시켜 M/A 조직 분율을 감소시켰으며, 입계에 조대하게 형성되어 충격특성을 저하시키는 NbC 등의 형성 억제를 위해 Nb의 첨가를 생략하였다. Fig. 14는 25t 두께의 HSA500 강재를 200 kJ/cm의 입열로 SAW 1 Pass 적용한 마크로 사진과 함께, 그 마이크로 미세조직을 SM490B 강재와 비교하여 나타낸 것으로 HSA500 강재의 경우 조대결정립 열영향부의 결정립 크기가 훨씬 더 미세함을 확인할 수 있다.
4. 교량용 강재 / 용접기술
Table 4는 국가별 교량용 강재의 규격을 나타낸다. 우선 일본 JFE/NSSMC社 등에서 개발된 교량용 강재의 경우, 일반교량용강과 내후성강 (W)으로 구분되며 각각에 대해 예열이 불필요한 타입 (EX), 대입열이 가능한 타입 (EG) 등으로 세분화 되어있다. 1960년도에 “Road bridge spec.”에 교량용 강재에 대한 규격이 제정되었고, SM 규격 (JIS G3106)에 부합하는 강재를 사용토록 하였는데, 기존 SM 규격에 명시된 것 이상의 성능이 요구되어 Nippon steel에서 BHS (Bridge High performance Steel)를 개발하게 되었다18). 2008년도에 보고된 연구에 따르면, 교량용 강재의 대다수를 차지하는 거더교 (Girder bridge)의 효과적인 사용을 위한 항복강도 상한치는 500 MPa이었으나, 이후 Honshu-Shikoku bridge에 고강도 BHS (YS: 680 MPa, TS: 780 MPa)가 적용되면서 700 MPa급 강재 적용이 제안되었다19).

Development of bridge steels according to regional standards (EX: Preheat insensitive, EG: High heat input, HSB: High strength rolled Steel for Bridge)
국내 교량용 강재의 경우, HSB 500, 600, 800급 강재로 구분되며 각각에 대해 일반교량용, 저온인성용 (L), 내후성용 (W)으로 구분된다. 저온인성용의 경우, -20 °C에서 충격인성 값 47J 이상을 보증하며, HSB800L의 경우, -40 °C에서 충격인성 값 47J 이상을 보증하도록 개발되었다. 내후성강의 경우에도, HSB 500, 600, 800급까지 개발되어 일부는 양수대교 (경기도 양평) 및 오월교 (강원도 춘천) 등에 적용되었으나, 강재 표면 안정녹 형성과 관련한 미관상 극히 제한적으로만 적용이 이루어지고 있는 실정이다.
미국의 경우, 교량 맞춤형 고성능 강재 (High Performance Steel for Bridges)의 개발이 1992년부터 본격적으로 추진되었고, 2005년에는 연간 25천톤 규모 (전체 교량용 강재의 10%)의 HPS가 사용되고 있다. 일반 강재 대비 HPS 강재 적용 시, 대략 25%의 소요 강재 중량 감소 및 최대 18%의 건설비 절감이 가능한 것으로 알려져 왔다. 그리고, 신설 강교량의 45% 이상을 내후성강으로 적용하기도 하였으며, HPS 750 MPa급 이상의 강재는 QT로 생산하고 추세이다.
4.1 일반교량용 강
일본의 경우, 교량 제작 시, 일반적으로 SM570급 혹은 그 이상의 강도급의 강재를 적용할 경우, 저온균열 저감을 위해 예열이 요구된다. 용접생산성을 고려하여 Pcm을 0.2 이하로 조정 (탄소: 0.09%)하여 예열을 생략하거나 줄이는 방향으로 BHS 강재 (BHS500) 설계하여, 2012년 개통한 Tokyo Gate Bridge Truss 교에 BHS500 강재를 최초로 적용하여 대략 12% 수준의 비용 절감 효과를 거두었다. JFE/NSSMC 등에서 개발된 교량용 강재의 경우, 일반적으로 500 MPa급 강재의 경우 용접균열지수 값이 대략 0.2로 상당히 낮은 수준으로 예열이 불필요하며 최대 입열량이 100 kJ/cm에 이른다18). 이 경우, -5 °C에서 평가한 충격인성 값 또한 100 J 정도로 우수한 물성치를 보여준다. 700 MPa급의 경우, 용접균열지수 값이 대략 0.3~ 0.32 수준으로 50 °C 정도의 예열이 요구되며 -40 °C의 저온 충격인성 값, 100 J을 보증하기 위해 최대 입열량을 50 kJ/cm로 제한하고 있다18). 층간온도의 경우에도 기존 230 °C 이하에서 300 °C로 증가시킴에도 불구하고 충격치 47J 만족하도록 강재 및 용접부 설계가 이루어졌다. 특히 JFE에서 개발한 교량용 강재의 경우, 강재 생산 시 냉각속도와 미세조직 간 상관성을 배제시킬 수 있을 정도로 C 함량을 극저 (0.02 wt.%: 페라이트 내 최대 고용 한계치)로 관리하여, Super-OLAC 공정을 통해 개발을 진행하였고, 기본적으로 판 두께에 따른 강도편차가 거의 없는 것이 특징이다20). Fig. 15는 JFE 개발강재인 500 MPa급 교량용 강재의 미세조직과 용접부와 HAZ의 위치별 경도 값 및 충격 값을 보여준다. TMCP로 제조한 강재의 특성상 70 kJ/cm 정도의 입열 적용 시, 약간의 HAZ 연화가 발생하는 것을 확인할 수 있으나, 용접부와 HAZ의 충격인성 값은 대략 155 J을 넘는 수준이다.
국내의 경우, 고강도 교량용 강재의 대표적인 사례는 2000년도에 개통된 영종대교, 방화대교, 광안대교 등이 있다. 영종대교의 경우 국내 SM570 강재를 다량으로 사용한 강교량으로서 75t 이하의 판재의 50 °C 수준의 예열조건에서, 용접성 평가결과, FCAW (용접재료: Supercored81, 입열량: 12 kJ/cm) 및 SAW (용접재료: A3/S777MX, 입열량: 32 kJ/cm) 프로세스가 적용 시, -30 °C의 극저온에서 용접부 충격에너지 값이 각각 43 J과 57 J의 수준으로 나타났다21). 또한 POSCO社에서 개발한 교량용 강재, HSB600L의 경우, 용접부 최고경도 값이 대략 281 hv 수준으로 도로교 표준시방서에서 요구하는 기준 (≤370)을 충분히 만족하고 있고, 경사 y-groove 구속시험결과 40mm 두께의 경우 50 °C, 80mm 두께의 경우 75 °C의 예열이 요구되는 것으로, 비교적 양호한 저온균열저항성을 나타내었다5). Table 5에 HSB600L의 40mm와 80mm 각각에 대한 FCAW (입열량: 15 kJ/cm) 및 SAW (입열량: 50 kJ/cm) 프로세스 적용 시 평가된 기계적 물성을 요약하였다. 일반 교량용 HSB 600의 경우에는 SAW 기준 120 kJ/cm의 대입열 적용 시에도 규격 기준치인 0 °C, 47J의 충격인성 값에 비해 훨씬 높은 수준으로 평가되었고, HSB800급 강재의 경우에도, Table 6에서 확인할 수 있듯이, FCAW (입열량: 23 kJ/cm) 및 SAW (입열량: 50 kJ/cm) 적용 시, 인장강도 및 충격에너지 값이 규격 요구치를 모두 만족하고 있다.
4.2 내후성강
내식용 교량강재로 알려져 있는 내후성강의 내식 메커니즘의 경우, 스테인리스 강과 같이 표면 부동태 피막에 의한 부식저항성 향상 효과가 아닌, 저합금 성분계와 환경과의 반응으로 강재 표면에 형성되는 치밀한 안정녹에 의한 장벽 (Barrier) 효과에 기인한다22). 즉, 부식 초기에 형성되는 부식생성물 (γ-FeOOH)의 경우 구조 자체가 치밀하지 못하여 염화이온의 소지금속으로의 침투가 용이하지만 시간이 지나면서 보다 치밀한 형태의 부식생성물로 (α-FeOOH)로 변하여 추가적인 부식진행을 억제할 수 있다23). Fig. 16에 부식생성물 형성과 관련된 간단한 메커니즘을 도식화하여 나타내었다. 일반적으로 내후성강의 경우, 안정녹의 형성을 위해 크롬, 구리, 인, 니켈 등의 합금원소가 첨가된다. 특히 크롬의 경우 α-FeOOH 내 철 원자영역에 크롬이 부분적으로 대체되면서 α-(Fe1-xCrx)OOH되어 입자의 크기가 미세해지는 것으로 알려져 있다. 구리의 경우, 구리를 포함하는 부식생성물의 경우 전기전도성이 낮아, 전자의 이동을 수반하는 환원반응을 제어함으로써 부식저항성이 향상되는 효과가 있으며, 인의 경우 PO43-가 형성되어, 철 혹은 망간과 반응하여 용해성이 낮은 인산염 등을 형성하는 것으로 보고되고 있다2).
Nippon steel에서 개발한 BHS700W 강재의 경우, 1994년 Akashi Kaikyo Bridge에 적용된 바 있고, 50 °C의 예열 (저 탄소에 무 보론 성분계로, 기존 120 °C 예열에서 50 °C로 감소)과 50 kJ/cm의 입열이 적용될 수 있고, JIS 규격에서 요구하는 물성치 확보가 가능토록 설계되었다18).
5. 건축외장용 강재
5.1 강재개발 현황
Table 7은 국가별 개발된 도금재를 간략히 요약한 것으로, 보통 아연 혹은 알루미늄 단독의 1원계 도금재와, 아연-알루미늄 혹은 아연-마그네슘 합금의 2원계, 그리고 아연-알루미늄-마그네슘 의 3원계로 다양한 성분비로 개발되고 있다. 대개는 용융도금욕조를 통해 습식도금법 및 전기도금법으로 제조되며, 국가 및 철강사에 따라 상이한 방식의 물리증착법 (PVD)을 통해 도금재를 생산하기도 한다3). 도금층을 활용한 내식성 향상방법은 일반적으로 철에 비해 전위가 낮은 아연이 희생양극의 역할로 소지 철을 보호하는 메커니즘을 기본으로 한다. 또한 알루미늄 첨가에 따라 표면에 Al2O3의 치밀한 산화층이 부가적으로 형성되어 내식성을 향상시키기도 하며, 아연-알루미늄-마그네슘의 3원계 도금재의 경우, 마그네슘이 산화되어, Mg(OH)2를 형성하면서 다소 낮아진 pH에 기인해, 치밀한 구조의 Simonkolleite (Zn5(OH)8CI2·H2O)) 생성물이 표면을 덮어, 소지 철을 보호해주는 역할한다. 이를 통해, 아연 단독의 1원계 제품에 비해 표면 내식성이 대략 5~10배 가량 향상될 수 있다. Fig. 17은 1원계 도금재 (GI)와 3원계 도금재 (POSMAC: 아연-2.5%알루미늄-3%마그네슘) 표면에 형성되는 부식생성물의 형상을 비교하여 보여준다. 뿐만 아니라, 극표면에 형성되는 MgO의 경우, ZnO 혹은 Al2O3에 비해 전기전도성이 현저히 낮다24). 따라서 전자의 이동을 수반하는 환원반응을 보다 억제시킬 수 있다. 이와 같은 우수한 내식성을 보증할 수 있는 3원계 도금재로는 일본 Nishin steel에서 개발한 ZAM (아연-6%알루미늄-3%마그네슘), NSSMC에서 개발한 Superdyma (아연-11%알루미늄-3%마그네슘-0.2%실리콘), 유럽의 경우, ArceloMittal에서 개발한 ZM Coating (아연-3.7%알루미늄-3%마그네슘) 등이 있고, 주로 건축용 외장재로서 축사, 태양열발전 하부지지대, 물탱크, 가드레일 등에 적용되고 있다.
5.2 용접성 및 용접이용기술
도금재의 우수한 내식성에도 불구하고 실제 건축용 외장재 등으로 적용함에 있어 중요한 문제점으로 지적되는 것은 용접 시 작업성 저하와 함께, 용접열에 의해 HAZ 도금층 기화로 인한 내식성 열화이다25). 용접 시, 융점 및 기화점이 낮은 도금층은 우선 기화하여 Spray mode로의 용적이행을 방해하면서 다량의 스패터와 함께 흄이 발생하여 용접작업을 어렵게 만든다. 또한 용접부와 HAZ의 경우, 내식성 보완을 위해 후처리 (은분 Spray 혹은 용사 작업)가 부가적으로 요구되어 작업 생산성을 떨어뜨린다. Fig. 18은 3원계 도금재인 POSMAC의 용접 후 용접부와 열영향부의 표면 마크로 형상 및 단면 형상과 성분분석 결과를 보여준다. 본 문제에 대해 국내 POSCO社에서는 2단 펄스 용접기를 활용하여 Spray mode로의 용적이행을 유도하거나 후처리 방법을 개발 중에 있고, 스테인리스 용접재료를 적용하여 후처리를 생략한 용접방법 등을 검토 중에 있다. 일본 NSSMC의 경우, Seamless 타입의 Flux cored wire로서, 고 크롬 스테인리스 용접재료 (FC-309SD)를 적용하여 후처리 없이 용접부와 HAZ 내식성을 보증할 수 있음을 보고하였다25). Fig. 19에서는 용접재료로서 기존 탄소강을 적용한 경우와 스테인리스강을 적용한 경우에 있어 염수분무실험 (Salt Spray Test) 1000 hr 후의 결과를 보여준다. 물론 스테인리스 용접재료를 적용하는 경우, 용접금속 내 미세조직의 페라이트 분율을 35% 이하로 설계하면 아연에 의한 LME (Liquid Metal Embrittlement)가 Fig. 20과 같이 발생할 수 있으므로, 최근 POSCO社에서는 용접부 내식성 향상과 함께 LME 저항성 유지를 위해 듀플렉스 타입의 스테인리스 용접재료를 개발하여 현재 저원가로 최적화 작업 중에 있다.
6. 결 론
본 기고에서는 건축 및 교량 분야에 적용되고 있는 다양한 강재들의 특성 및 용접기술에 대한 논의를 진행하였다. 초고층화, 장스팬화, 안전화, 장수명화로 설명될 수 있는 건축/교량 분야에서, 현재 요구되고 있는, 그리고 향후 요구될 성능 및 물성확보를 위해, 고강도를 비롯한 고성능 강재 뿐 아니라 효과적인 용접시공기술이 적극적으로 개발되어야 할 것이다. 즉, 고강도/고성능 강재, 대입열을 비롯한 고효율 용접시공기술과 함께 흡습을 최소화할 수 있는 Seamless 타입의 우수한 용접재료 등의 개발이 복합적으로 이루어져야 할 것이다.